以某家涂料生產(chǎn)企業(yè)為例,分析大風量、低濃度非連續(xù)排放有機廢氣治理技術的經(jīng)濟性。結(jié)果發(fā)現(xiàn):(1)對于大風量、低濃度有機廢氣,在幾種主流治理技術中,當回收液具有利用價值時,"活性炭吸附-氮氣脫附冷凝溶劑回收技術"相較"RTO(蓄熱式熱氧化)技術"、"沸石轉(zhuǎn)輪吸附濃縮-RTO技術"及"沸石轉(zhuǎn)輪吸附濃縮-CO(催化氧化)技術"的經(jīng)濟性更優(yōu);而回收液需作為危廢處置時,"沸石轉(zhuǎn)輪吸附濃縮-CO技術"更具經(jīng)濟性,但必須考慮來氣的情況,選擇合適的催化劑,確保系統(tǒng)運行的穩(wěn)定性。(2)對于非連續(xù)排放的廢氣,"分散收集,集中處理"的治理模式有利于降低VOCs治理裝置投資成本,具有很好的經(jīng)濟性。
揮發(fā)性有機物( VOCs) 作為光化學反應的重要前體物,是產(chǎn)生灰霾的主要根源,不僅危害環(huán)境而且危害人類健康,近年來受到社會高度重視,VOCs治理迅速掀起了一股熱潮。
VOCs治理技術有吸附、冷凝、吸收、膜分離等回收技術,以及燃燒、生物、低溫等離子體、紫外光催化氧化等消除技術,以及根據(jù)廢氣特點采取組合技術。近年來,對于大風量、低濃度有機廢氣,治理的主流技術有“RTO ( 蓄熱式熱氧化) 技術”“沸石轉(zhuǎn)輪吸附濃縮- RTO 技術”“活性炭吸附- 氮氣脫附冷凝溶劑回收技術”和“吸附濃縮- CO ( 催化氧化) 技術”,廣泛運用于汽車涂裝廢氣、家具廠噴漆廢氣、包裝印刷廢氣、涂料生產(chǎn)廢氣等的治理。
企業(yè)在選擇VOCs 治理技術時,必須兼顧技術可行性和經(jīng)濟適宜性,昂貴的投資和較高的運行費用對于很多企業(yè)來說難以承受。涂料生產(chǎn)廢氣是典型的大風量、低濃度有機廢氣,因此,本文以非連續(xù)生產(chǎn)的某涂料生產(chǎn)企業(yè)為例,比較幾種可行技術方案的經(jīng)濟性,為優(yōu)化VOCs 治理方案提供參考。
1 VOCs治理技術經(jīng)濟性分析
1. 1 各技術工藝簡介
1. 1. 1 RTO技術
RTO 是一種配有蓄熱床層的熱力燃燒治理技術,蓄熱燃燒系統(tǒng)主要由燃燒裝置、蓄熱室( 內(nèi)有蓄熱體) 、換向系統(tǒng)、排煙系統(tǒng)和連接管道等組成( 見圖1) ,其工作原理為: 將有機廢氣加熱至750℃以上,使廢氣中的有機物氧化分解成CO2和H2O,氧化反應產(chǎn)生的高溫氣體流經(jīng)蓄熱體,使蓄熱體升溫而“蓄熱”,進而用于預熱后續(xù)進入的有機廢氣而“放熱”,從而節(jié)省廢氣升溫所消耗的燃料量,蓄熱體“放熱”后立即引入適量潔凈空氣進行清掃,待清掃完成后才能進入“蓄熱”程序。三室RTO 是目前主流的應用裝置,蓄熱體分為三個室,每個室依次經(jīng)歷“蓄熱—放熱—清掃”等程序,如此反復。由于蓄熱系統(tǒng)的熱回收效率很高,該技術可對具有一定濃度的連續(xù)排放的有機氣體進行高效且較經(jīng)濟的處理。
1. 1. 2 催化氧化技術
催化氧化系通過催化劑的作用減低揮發(fā)性有機物的氧化反應所需的溫度,與直接燃燒相比,由于燃燒溫度較低,對設備材料和保溫的要求相應減低,同時排氣溫度通常也低于直接燃燒,達到一定的節(jié)能效果,總體占地面積小,風量不大時投資相對較小。催化氧化工藝流程見圖2,催化工藝在選擇催化劑時需要全面考慮來氣的情況,確保催化劑在使用過程中不出現(xiàn)失活現(xiàn)象才能達到設計的性能和催化劑使用壽命。由于采用的是間壁式換熱裝置,其熱回收率要大大低于RTO。
1. 1. 3 沸石轉(zhuǎn)輪吸附濃縮-RTO ( 或CO) 技術
該技術是沸石轉(zhuǎn)輪吸附同RTO ( 或CO) 技術的組合工藝,系統(tǒng)主要由粉塵過濾器、沸石轉(zhuǎn)輪濃縮吸附裝置、RTO ( 或CO) 、風機、換熱器、PLC自動化控制系統(tǒng)等組成( 見圖3) 。該組合技術通過沸石轉(zhuǎn)輪的吸附濃縮使大風量、低濃度有機廢氣濃縮為較小風量的高濃度氣體,高濃度氣體再經(jīng)RTO 或CO 高溫氧化分解為CO2和H2O。轉(zhuǎn)輪的工作原理為: 轉(zhuǎn)輪以一定轉(zhuǎn)速連續(xù)旋轉(zhuǎn),轉(zhuǎn)過吸附區(qū)、脫附區(qū)和冷卻區(qū),有機廢氣在吸附區(qū)被吸附凈化,吸附在轉(zhuǎn)輪中的有機物在脫附區(qū)被熱風脫附濃縮后進入RTO 或CO,脫附后的轉(zhuǎn)輪轉(zhuǎn)到冷卻區(qū)被冷卻,再旋轉(zhuǎn)至吸附區(qū),持續(xù)吸附VOCs 廢氣,周而復始,連續(xù)工作。
1. 1. 4 活性炭吸附- 氮氣脫附冷凝溶劑回收技術
該技術是活性炭吸附與冷凝的組合工藝,系統(tǒng)主要由粉塵過濾器、顆?;钚蕴课窖b置、氮氣脫附系統(tǒng)、風機、冷凝系統(tǒng)、PLC 自動化控制系統(tǒng)等組成( 見圖4) 。該組合技術通過活性炭吸附- 高溫氮氣脫附使大風量、低濃度有機廢氣濃縮為高濃度氣體,高濃度氣體再經(jīng)冷凝系統(tǒng)冷凝成溶劑并回收。脫附再生后的活性炭再繼續(xù)用于VOCs 廢氣的吸附。
1. 2 案例的技術經(jīng)濟性分析比較
根據(jù)某涂料生產(chǎn)企業(yè)廢氣的排放情況,采用以上主流工藝設計若干可行的技術方案,并通過各技術方案的投資和運行費用等分析比較,從技術經(jīng)濟性角度進行方案優(yōu)選。
樣本企業(yè)VOCs 廢氣情況: 廢氣排口有5 個,三個車間,車間排口數(shù)分別為2 個、2 個、1 個,由于涂料生產(chǎn)的特點,排放VOCs 氣體的濃度不穩(wěn)定,約100 ~ 400mg /m3。該企業(yè)每周生產(chǎn)5d,每天生產(chǎn)8h,VOCs 廢氣具有大風量、低濃度、非連續(xù)穩(wěn)定排放的特點。
結(jié)合廢氣污染源的情況,設計了7 種備選方案,如下:
方案A 配置5 套處理能力25 000m3 /h 的RTO;
方案B 配置5 套處理能力25 000m3 /h 的轉(zhuǎn)輪濃縮加3 000m3 /h 的RTO;
方案C 配置2 套處理能力50 000m3 /h 的轉(zhuǎn)輪濃縮加5 000m3 /h 的RTO,1 套處理能力25 000m3 /h 的轉(zhuǎn)輪濃縮加3 000m3 /h 的RTO;
方案D 配置5 套處理能力25 000m3 /h 的活性炭吸附- 氮氣脫附冷凝溶劑回收裝置;
方案E 配置2 套處理能力50 000m3 /h 的活性炭吸附- 氮氣脫附冷凝溶劑回收裝置,1 套處理能力25 000m3 /h 的活性炭吸附- 氮氣脫附冷凝溶劑回收裝置;
方案F 配置5 套處理能力25 000m3 /h 的轉(zhuǎn)輪濃縮加3 000m3 /h 的CO;
方案G 配置2 套處理能力50 000m3 /h 的轉(zhuǎn)輪濃縮加5 000m3 /h 的CO,1 套處理能力25 000m3 /h 的轉(zhuǎn)輪濃縮加3 000m3 /h 的CO。
考慮到生產(chǎn)為非連續(xù)性,按每天排放8h,平均排氣濃度250mg /m3 考慮。方案A、B、C 中的RTO 每天啟爐一次。方案B、C 中的轉(zhuǎn)輪濃縮加RTO 系統(tǒng)正常運行時,由于增濃后的氣體濃度達到RTO 自持氧化濃度范圍,不考慮濃縮后氣體的RTO 輔助燃料費用,僅考慮轉(zhuǎn)輪濃縮的加熱附加燃料費用。由于風量大濃度低且間歇運行,方案D、E 按每5d 保護作用時間的吸附容量設計,每套系統(tǒng)配備由兩臺并聯(lián)吸附床構(gòu)成的可就地再生吸附凈化系統(tǒng),生產(chǎn)擴產(chǎn)時可實現(xiàn)連續(xù)運行。方案F、G 的CO 也是每天啟爐一次,但需要補充一定量的燃料以維持CO 的正常運行。
對于RTO 系統(tǒng),其直接運行費用包括風機及輔助系統(tǒng)的電費、輔助燃料費( 包括啟動加熱和進氣濃度不高時的輔助加熱) 和運行維護人員費用。對于風量25 000m3 /h 的RTO,其裝機功率按55 kW 計,進氣濃度按平均250mg /m3 考慮; 對于5 000 m3 /h 的RTO,其裝機功率按22kW 計,不考慮輔助燃料消耗; 對于3 000m3 /h 的RTO 的功率按12kW 計,也不考慮輔助燃料消耗??紤]到RTO系統(tǒng)每天的啟動加熱操作,每天運行按10h 計。由于是非連續(xù)運行,每臺RTO 均考慮每天啟動烘爐的燃氣消耗,烘爐燃氣量參照RTO 的供應商提供的數(shù)據(jù)估算。
對于25 000m3 /h 轉(zhuǎn)輪濃縮系統(tǒng),兼顧3 級預處理過濾的阻力及再生氣體的動力等,主風機、輔助風機等功率按20kW 計; 50 000m3 /h 轉(zhuǎn)輪濃縮系統(tǒng),按35kW 計,由于進氣濃度較低,均考慮了脫附加熱所需的燃氣消耗。
25 000m3 /h 活性炭吸附系統(tǒng)的吸附風機功率按22kW 計,每天按8h 運行時間計,再生系統(tǒng)裝機功率75kW ( 含制冷系統(tǒng)) 。方案D 按平均每天再生一套、每次再生5h 設計,再生過程采用的高溫氮氣用蒸汽加熱,再生耗蒸汽量每次按1. 5t 計。
方案E 為2 套50 000m3 /h 和1 套25 000m3 /h 的活性炭吸附加氮氣脫附裝置,3 套系統(tǒng)每周各再生1次,費用平均到5d 得到日運行費用。
對于CO 系統(tǒng),其直接運行費用包括風機及輔助系統(tǒng)的電費、輔助燃料費( 包括啟動加熱和輔助加熱) ,催化劑運行20 000h 后的更換費用和運行維護人員費用。對于5 000 m3 /h 的CO,其裝機功率按5. 5kW 計,輔助燃料消耗按進出口溫差140℃計; 對于3 000m3 /h 的CO 的功率按4kW 計,輔助燃料消耗按進出口溫差140℃計??紤]到CO系統(tǒng)每天的啟動加熱操作,每天運行按8. 5h 計。由于是非連續(xù)運行,每臺CO 均考慮每天啟動烘爐的燃氣消耗,烘爐燃氣量按將催化床加熱到300℃時的熱量平衡數(shù)據(jù)估算。
由于RTO、轉(zhuǎn)輪濃縮加RTO 以及轉(zhuǎn)輪濃縮加CO 涉及的熱氧化系統(tǒng)套數(shù)多,且需要每天啟動時加熱爐體,工作時間較長,需3 ~ 4 人運行。再生式活性炭系統(tǒng),為全自動運行,盡管再生時需要值守,方案D、E 因采用的是就地再生,只需配備1人即可操作運行。電費按0. 8 元/kW·h 計,天然氣按3. 5 元/m3 計,蒸汽按0. 3 元/kg 計,人員費用按300 元/d 計。
基于以上方案及基礎數(shù)據(jù),可得到不同方案的運行費用( 表1) 。表1 中系統(tǒng)的投資費用由于涉及到技術專利、材質(zhì)、設備及自控元器件等配置的差異,結(jié)合供應商的詢價,給出了大致的價格區(qū)間。
在表1 投資費用基礎上取中間值,并按10 年使用壽命,5%的利率及每年工作250d,平均設計濃度250mg /m3,回收率90% 等條件計算出的年度直接費用、間接費用和年度總費用情況如表2 所示。其中活性炭方案D、E 分別給出了回收液回用( D1、E1) 和作為危廢處置( D2、E2) 兩種情況的費用,回收液可用價格取5 000 元/t,危廢處理費按8 000 元/t 計。
方案A 對于低濃度且非連續(xù)排放的氣體采用RTO 工藝,一方面RTO 的氣流阻力較大,濃度低時需要添加輔助燃料,同時間歇運行,每天均需要進行啟動升溫,總體上非常不經(jīng)濟。
方案B 采用沸石轉(zhuǎn)輪濃縮加RTO 的方式,由于濃縮系統(tǒng)的流體阻力較小,故有效地減少了主體氣流的阻力,同時濃縮后的氣體再進行熱氧化減少了熱氧化的輔助燃料需求,但每天的啟爐和轉(zhuǎn)輪的熱再生需要消耗一定的動力能源。
方案C 系根據(jù)樣本企業(yè)的實際情況進行的優(yōu)化,通過合并系統(tǒng)的規(guī)模效應提高了技術經(jīng)濟性。
方案D 配置活性炭吸附氮氣保護脫附系統(tǒng),因吸附凈化阻力不大,總體運行成本*低,由于活性炭系統(tǒng)的吸附能力,與熱氧化系統(tǒng)相比更加適用于非連續(xù)排放過程,但因工藝復雜及安全配置的因素,投資費用不低。該系統(tǒng)主要用于溶劑回收,進口氣體濃度高時,技術經(jīng)濟性更佳。對于樣本企業(yè),回收的溶劑可用于低端產(chǎn)品制造。因此D1 方案情景總體年度費用較熱氧化方案具有優(yōu)勢。如表2所示,如果回收液無法利用,則還需要考慮將收集液體作為危廢的處置的運行費用,如D2 方案情景所示,活性炭吸附氮氣保護脫附系統(tǒng)的運行費用要超過濃縮熱氧化系統(tǒng)。
方案E 為方案D 根據(jù)企業(yè)情況的優(yōu)化版,通過合并系統(tǒng)的規(guī)模效應提高了總體的技術經(jīng)濟性。方案E1 情景在所有方案情景中總年度費用*低。
方案F 為沸石轉(zhuǎn)輪濃縮加CO 的方式,與方案B 相比,由于CO 床層阻力較RTO 要小,所以總體電耗減低,但由于通常情況下催化燃燒的熱回收率要遠低于RTO,所以需要添加一部分輔助燃料,因此總體動力費用差距不大。但考慮到催化劑的更換費用,總體直接運行費用要高于RTO。CO 系統(tǒng)在小風量情況下的投資要小于RTO,因此總年度費用總體較低。但使用CO 設備時,在控制催化劑失活保證系統(tǒng)性能穩(wěn)定性方面需要特別注意。
方案G 為方案F 根據(jù)企業(yè)情況的優(yōu)化版,通過合并系統(tǒng)的規(guī)模效應提高了總體的技術經(jīng)濟性。
從表2 可知,對于樣本企業(yè),“RTO 技術”投資和運行費用*高,在回收液可以回用于生產(chǎn)時,“沸石轉(zhuǎn)輪吸附濃縮- RTO 技術”及“沸石轉(zhuǎn)輪吸附濃縮- CO 技術”投資和運行費用也明顯高于“活性炭吸附- 氮氣脫附冷凝溶劑回收技術”。所以,就樣本企業(yè)的情況而言,從經(jīng)濟性角度,優(yōu)先采用“活性炭吸附- 氮氣脫附冷凝溶劑回收技術”,且方案E 優(yōu)于方案D。
2 治理模式改進
2. 1 “分散收集,集中處理”模式
根據(jù)前述技術經(jīng)濟性分析,選用“活性炭吸附- 氮氣脫附冷凝溶劑回收技術”對樣本企業(yè)廢氣進行治理。
考慮到間歇排放且VOCs 排放負荷較低,為了進一步減少投資,同濟大學提出“分散收集,集中處理”的區(qū)域范圍VOCs 減排控制模式,即方案H,配置7 套( 5 用2 備) 處理能力25 000m3 /h 移動式活性炭吸附裝置和1 套活性炭裝置再生中心,該方案中“分散收集”指采用5 個移動式活性炭吸附裝置分別對5 個排口VOCs 廢氣進行吸附凈化,當吸附一段時間后,在線監(jiān)控設施顯示排口VOCs 濃度接近60% ~ 80% 的排放限值時,將移動式活性炭吸附裝置運送到廠內(nèi)集中建設的一套“氮氣脫附冷凝溶劑回收系統(tǒng)”的活性炭裝置再生中心進行脫附再生,同時排口處更換一個再生過的移動式活性炭吸附裝置。
方案H 和方案D 規(guī)模和再生頻次相似,只是方案H 需要進行吸附器的移動,活性炭吸附系統(tǒng)排氣點處為吸附過程,無需人員運行看管。系統(tǒng)運行時,每天的主要工作為1 臺吸附裝置的更換移動及再生中心5h 的再生,系統(tǒng)的運行和維護按2 人計。方案H 的年度費用情況見表3,投資費用在500 ~ 700 萬元之間,盡管人工費用有所增加,但總體年度費用仍然明顯低于方案D、E。
方案H 主要針對間歇生產(chǎn)的特點,采用可移動式活性炭吸附裝置加集中再生的模式進一步提高了技術經(jīng)濟性。由于生產(chǎn)裝置運行前不需要特別提前對環(huán)保裝置進行預熱,集中再生可有效提高再生裝置的使用效率,特別適合于大風量、低濃度非連續(xù)排放的污染源的控制。該模式突破了常見的活性炭吸附- 脫附一體化就地處理的模式,大大減少了建設造價。
該治理模式控制的關鍵是對廢氣排口VOCs 濃度進行實時監(jiān)控,樣本企業(yè)采用較經(jīng)濟且維護較簡單、便捷,使用相對安全的光離子氣體檢測儀( PID) 進行內(nèi)控監(jiān)測。監(jiān)測數(shù)據(jù)可以在手機應用程序上實時查看,一旦數(shù)據(jù)達到設定的監(jiān)控上限值時,就更換移動式活性炭吸附裝置。
2. 2 實際運行效果說明
方案H 實施后,為了驗證該治理工藝的治理效果,樣本企業(yè)委托第三方對5 個廢氣排口進行了監(jiān)測,移動式活性炭吸附裝置進出口非甲烷總烴的監(jiān)測結(jié)果見表4,結(jié)果顯示廢氣經(jīng)治理后5 個排口非甲烷總烴均能達標排放,且在一定條件下,非甲烷總烴的去除效率能達90%以上。
方案H 實施后,樣本企業(yè)的實際投資和運行費用與方案H 預期相差不大( 見表4) ,由于樣本企業(yè)實際生產(chǎn)負荷低,產(chǎn)生的廢氣濃度低,且非連續(xù)穩(wěn)定排放,日回收溶劑量為86. 2 kg,回收溶劑用于低端產(chǎn)品生產(chǎn),可產(chǎn)生431 元/d 的經(jīng)濟效益( 見表5) 。
2. 3 移動式治理模式的應用前景
活性炭吸附技術是簡單易行的治理技術,是一些分散的諸如噴涂、印刷、化工等小型企業(yè)首選的治理技術。但單個企業(yè)建設相應的活性炭再生系統(tǒng)費用高,小企業(yè)往往難以承擔。如果采用更換活性炭的方式,新活性炭購買和廢活性炭作為危廢處置的費用均很高。因此,要減輕單個企業(yè)的治理費用,可采用移動式治理模式,將吸附飽和的活性炭,送到統(tǒng)一建設的活性炭異位( 地) 再生平臺進行再生,大大減少單個企業(yè)的投資費用。也可采用“吸附- 移動脫附”的VOCs 凈化技術,廢氣收集后經(jīng)多級過濾裝置去除漆霧、顆粒物,再經(jīng)分子篩吸附床吸附后達標排放。吸附床吸附飽和后由移動式解吸裝置原位脫附,脫附出的VOCs 經(jīng)催化燃燒裝置凈化處理。
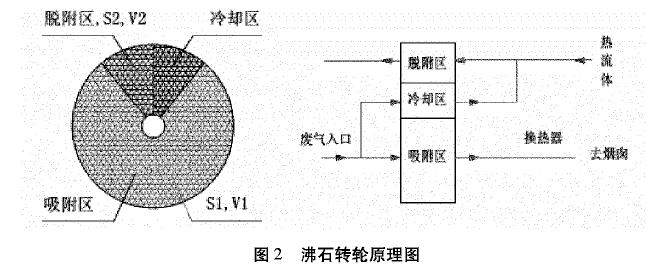
總之,無論是異位脫附還是原位脫附的移動式治理模式,都是打破傳統(tǒng)的吸附- 脫附一體化模式,優(yōu)化吸附劑再生方式,具有更好的經(jīng)濟性,尤其適用于非連續(xù)排放的廢氣。
3. 1 對于大風量、低濃度有機廢氣,在幾種主流治理技術中,當回收液具有利用價值時,“活性炭吸附- 氮氣脫附冷凝溶劑回收技術”相較“RTO”“沸石轉(zhuǎn)輪吸附濃縮- RTO 技術”及“沸石轉(zhuǎn)輪吸附濃縮- CO 技術”的經(jīng)濟性更優(yōu); 而回收液需作為危廢處置時, “沸石轉(zhuǎn)輪吸附濃縮- CO 技術”更具經(jīng)濟性,但必須考慮來氣的情況,選擇合適的催化劑,確保系統(tǒng)運行的穩(wěn)定性。
3. 2 對于非連續(xù)排放的廢氣, “分散收集,集中處理”的治理模式有利于降低VOCs 治理裝置投資成本,具有很好的經(jīng)濟性。
版權聲明:本網(wǎng)注明來源為“環(huán)亞環(huán)?!钡奈淖?、圖片內(nèi)容,版權均屬本站所有,如若轉(zhuǎn)載,請注明本文出處:http://ujianfei.com 。同時本網(wǎng)轉(zhuǎn)載內(nèi)容僅為傳播資訊,不代表本網(wǎng)觀點。如涉及作品內(nèi)容、版權和其它問題,請與本網(wǎng)站聯(lián)系,我們將在及時刪除內(nèi)容。